Software-Defined Vehicles: Very real when tire monitoring is transformed
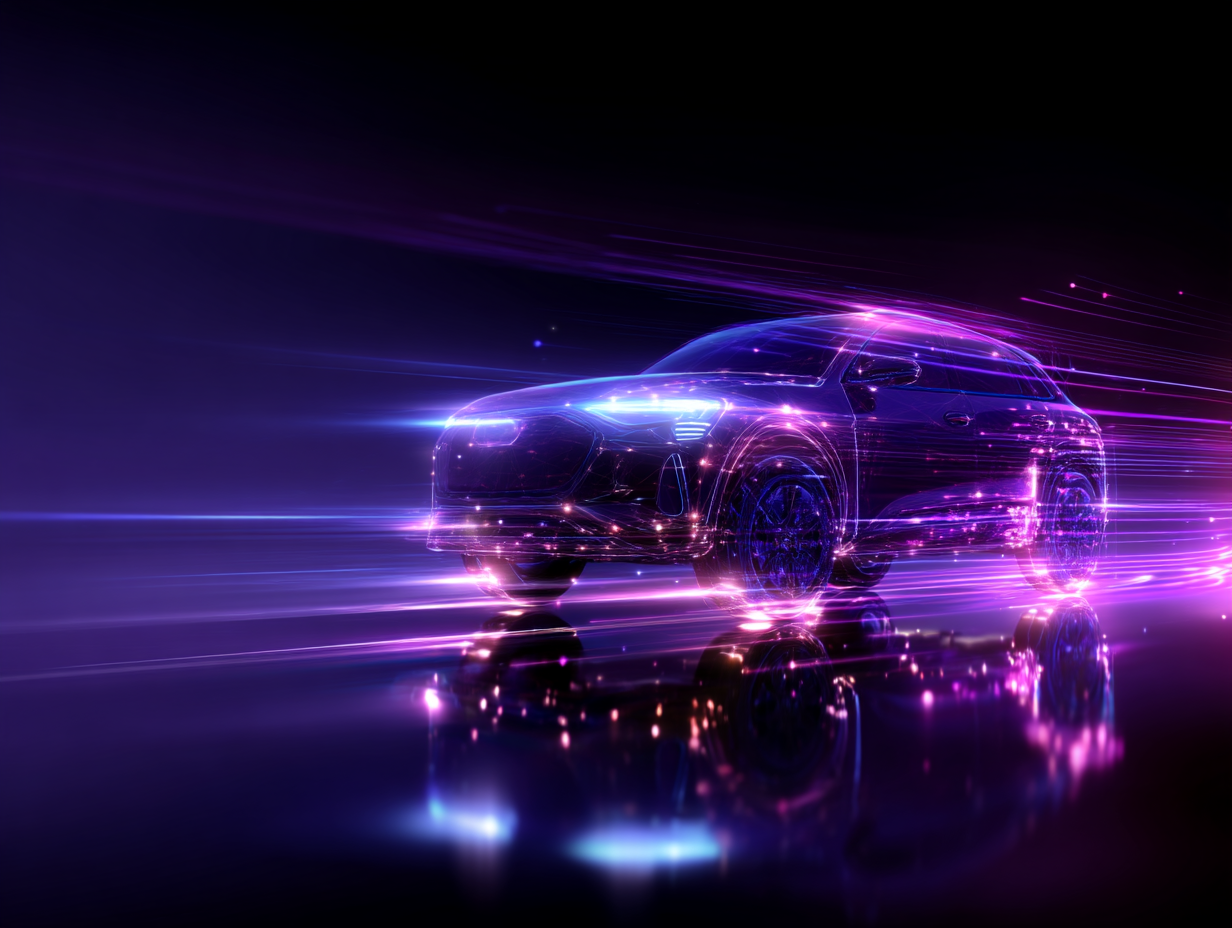
For over a century, automotive innovation was defined by mechanical engineering. Today, vehicles are increasingly defined by their software.
The automotive industry stands at a pivotal moment. After more than a century of hardware-driven innovation focused on engines, transmissions, and mechanical improvements, we are at a big shift: software has become the defining force in vehicle development and differentiation. The traditional car manufacturers are trying to change, keeping up with new players, implementing software first strategies. This transformation has introduced what we now call the Software-Defined Vehicle (SDV) — a vehicle where features, performance, user experience, and services are powered primarily by code rather than hardware components.
According to recent industry estimates, modern vehicles contain up to 150 million lines of code — more than a commercial airliner. By 2030, experts project that software will account for 60% of a vehicle's value, up from roughly 10% in 2000. This transformation isn't merely incremental; it represents a complete paradigm shift in how vehicles are conceived, developed, maintained, and experienced.
The Hardware-to-Software Revolution
Traditionally, vehicles were assembled from thousands of mechanical components and dozens of Electronic Control Units (ECUs), each responsible for specific functions such as engine control, infotainment, or braking. These systems operated in silos, creating complex architectures with limited ability to communicate or evolve after production. The result was vehicles that remained largely static throughout their lifecycle, with capabilities fixed at the moment they left the factory.
Today's software-defined vehicles invert this model. Rather than designing software to match hardware, automakers now design hardware to support flexible, upgradable software platforms. High-performance computing units replace dozens of ECUs, enabling more efficient communication, integration, and long-term adaptability. Like smartphones, SDVs can evolve over time through over-the-air updates, gaining new features and improving existing ones throughout their lifecycle.
Tire Monitoring: A small part of the transformation
To understand this shift in concrete terms, consider the evolution of Tire Pressure Monitoring Systems (TPMS). These safety systems exemplify the hardware-to-software transformation reshaping the automotive industry.
The first generation of TPMS relied exclusively on hardware — direct TPMS (dTPMS) systems with physical pressure sensors inside each tire transmitting readings to a receiver. While effective at monitoring pressure, these systems added complexity, cost, and maintenance requirements to the vehicle. Each sensor required batteries, RF components, and physical installation, creating points of failure and generating electronic waste when sensors needed replacement every 5-7 years.
At NIRA Dynamics, we pioneered an alternative approach: indirect TPMS (iTPMS) that leverages software intelligence rather than additional hardware. Our Tire Pressure Indicator (TPI) technology uses advanced algorithms to analyze existing wheel speed signals from the vehicle's ABS sensors. By detecting subtle variations in wheel rotation patterns and applying sophisticated signal processing, TPI can accurately determine when tires are underinflated — without requiring any sensors inside the tires.
This approach exemplifies the software-defined vehicle paradigm: using intelligence rather than components to deliver critical functionality. The advantages mirror those of the broader SDV revolution:
- Reduced complexity: No additional hardware components to manufacture, install, or maintain
- Environmental benefits: With over 110 million vehicles now using our iTPMS technology, we've eliminated an estimated 40,000 tons of electronic waste from sensor batteries and components
- Lower lifetime costs: No sensor replacements needed throughout the vehicle's life
- Continuous improvement: Software algorithms can be refined through updates, improving performance over time
- Seamless integration: Works with existing vehicle architecture and can be deployed through standardized interfaces
Technical Evolution: From Simple Detection to Intelligent Monitoring
The technical evolution of iTPMS mirrors the broader advances in automotive software systems. Early indirect systems used basic algorithms that could only detect significant pressure differences between wheels, limiting their effectiveness when all tires lost pressure equally. Critics rightfully pointed out these limitations.
Modern iTPMS, however, represents a quantum leap in capability. Today's systems employ multi-sensor fusion, advanced statistical models, and machine learning techniques to detect subtle patterns that indicate pressure loss across all tires. They can determine not just that pressure is low, but precisely which tire is affected and by how much. The latest generation of our TPI UX technology provides drivers with percentage-based pressure readings comparable to direct sensor systems, but without the associated hardware.
This progression from basic detection to sophisticated analysis exemplifies how software intelligence can match or exceed hardware-based approaches. The algorithms powering modern iTPMS can differentiate between normal variations (like those caused by temperature or road conditions) and genuine pressure loss, eliminating false alarms while providing reliable protection.
iTPMS in the Connected Vehicle Ecosystem
The true potential of software-defined vehicle systems emerges when they become part of a connected ecosystem. Here again, tire monitoring provides a compelling example. Beyond basic pressure warnings, modern iTPMS can contribute to a range of vehicle functions and services:
When integrated with cloud platforms, tire data becomes part of a broader predictive maintenance strategy. Patterns in pressure changes, combined with other vehicle signals, can predict tire wear and optimize replacement schedules. For fleet operators, this translates to reduced downtime and more efficient operations.
In advanced driver assistance systems (ADAS), accurate tire information improves traction control, stability systems, and braking. Our Tire Grip Indicator technology, for instance, uses the same wheel speed signals to estimate road friction conditions, providing critical input to safety systems without requiring additional sensors.
For electric vehicles, where efficiency directly impacts range, optimal tire pressure is particularly crucial. Software-based monitoring helps maintain ideal pressure, contributing to consistent range predictions and energy management.
"The most sustainable components are the ones you don't need to manufacture at all. Software-defined systems aren't just more efficient — they're fundamentally more aligned with circular economy principles."
Meeting and Exceeding Regulatory Requirements
One common misconception about software-based systems is that they might not meet the same regulatory standards as hardware alternatives. In reality, modern iTPMS not only meets but often exceeds regulatory requirements.
Our TPI technology complies with all global TPMS regulations, including FMVSS138 in the United States and ECE R141 in Europe. These standards focus on performance outcomes — detecting underinflation reliably and alerting drivers appropriately — rather than specifying implementation methods. By meeting these performance standards without additional hardware, iTPMS delivers regulatory compliance more efficiently.
This illustrates a broader principle of software-defined vehicles: regulations should be technology-neutral, focusing on safety outcomes rather than prescribing specific hardware implementations. As vehicles become more software-defined, this approach will become increasingly important for balancing innovation with safety.
The Future: Software-Defined Safety
Looking ahead, we see software intelligence transforming vehicle safety systems more broadly. The principles that make iTPMS effective — using existing signals and sophisticated algorithms rather than dedicated hardware — can be applied to numerous safety functions.
Take our Loose Wheel Indicator technology, which detects the early signs of wheel detachment by analyzing vibration patterns in wheel speed signals. This potentially life-saving feature requires no additional hardware, yet provides protection against a serious safety risk. Similarly, our Tread Wear Indicator uses existing vehicle data to monitor tire condition, alerting drivers before tires become dangerously worn.
The pattern is clear: software intelligence can deliver safety functions that would have previously required complex sensor arrays. This approach scales more efficiently across vehicle platforms, reduces points of failure, and enables continuous improvement through updates.
Strategic Implications for the Industry
The shift to software-defined vehicles has profound implications for automotive manufacturers, suppliers, and the broader ecosystem. For OEMs, it means rethinking development processes, organizational structures, and business models. Software expertise becomes as critical as mechanical engineering, requiring new talent and partnerships.
For suppliers, particularly traditional hardware manufacturers, this transformation presents both challenges and opportunities. Those that pivot to provide software solutions or hardware platforms optimized for software integration will thrive. Those that remain focused solely on components risk commoditization.
The aftermarket will also transform. With fewer physical components to replace and more functionality defined by software, service models will evolve. Over-the-air updates will replace some traditional service visits, while diagnostics will increasingly focus on software systems rather than mechanical components.
From an environmental perspective, software-defined vehicles represent a more sustainable approach to automotive technology. Reducing the number of physical components means less manufacturing impact, less waste, and more efficient resource use. Our experience with iTPMS demonstrates this clearly: eliminating sensors reduces raw material consumption, manufacturing energy, and end-of-life electronic waste.
Conclusion: Intelligence, Not Components
The automotive industry's future lies not in adding more hardware but in developing smarter software. From tire monitoring to advanced safety systems, the most innovative solutions today are those that leverage intelligence rather than components to deliver functionality.
At NIRA Dynamics, we've seen firsthand how this approach transforms vehicle systems. Our iTPMS technology, now installed in over 110 million vehicles worldwide, demonstrates that software-based solutions can deliver better performance, lower costs, and reduced environmental impact compared to hardware alternatives.
As vehicles become increasingly defined by software, this philosophy will extend to more systems and functions. The winners in this transformation will be those who understand that the best component is often the one you don't need at all — replaced by intelligence embedded in software.
The road ahead is clear: software-defined vehicles represent not just an evolution but a revolution in automotive technology. And sometimes, as our tire monitoring technology demonstrates, the most advanced solution is the one with fewer parts, not more.